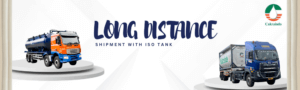
The transportation of bulk liquids, chemicals, and both hazardous and non-hazardous materials demands specialized containers to guarantee safety, efficiency, and adherence to international regulations. Two popular choices for this task are Lorry Tanks and ISO Tanks. Each option boasts unique advantages and is suited for different situations; however, the ideal choice may vary based on cargo type, distance, and available infrastructure. There are four key comparisons between ISO Tanks and lorry tanks, including cost efficiency, safety and security, capacity and volume, and transport flexibility.
1. Cost efficiency
Lorry Tank: For shorter, domestic routes, lorry tanks are usually more economical since they don’t rely on intermodal infrastructure. You only need one mode of transport (road transport)
ISO Tank: Although ISO Tanks provide flexibility and safety, they often come with higher costs due to the requirement for cranes, specialized handling equipment, and infrastructure to accommodate various transport modes. However, as the distance increases and shipments become larger, the cost per unit of liquid transported generally decreases.
If cost-saving is your primary goal for shipments over short distances, then a lorry tank is likely your best option. Conversely, for longer distances and international shipping, an ISO Tank proves to be more economical, especially when the benefits of multimodal transportation outweigh the handling costs.
2. Safety and Security
Lorry Tank: Although contemporary Lorry Tanks are constructed with durable materials and equipped with safety features such as pressure relief valves and compartments, they remain vulnerable to accidents caused by road hazards, like collisions, which may lead to spills or leaks.
ISO Tank: ISO Tanks are subject to strict regulations and engineered for strength, durability, and leak-proof performance. They provide exceptional protection and are built to endure extreme conditions, such as during shipping and handling. Featuring double-layered walls and secure fittings, they meet international safety standards for the transport of hazardous materials.
Lorry Tanks are built with strong construction and safety features to ensure adequate protection during road transport. However, their susceptibility to road accidents stems from various unpredictable factors, including road conditions, the behavior of other drivers, liquid sloshing, and environmental influences. These inherent risks associated with road transport make Lorry Tanks more likely to encounter accidents compared to the more controlled settings of rail or sea transport utilized by ISO Tanks.
3. Capacity and Volume
Lorry Tank: Typically, Lorry Tanks are designed for short to medium-distance transport and have a capacity ranging from 10,000 liters to 30,000 liters, depending on the size, customization and type of truck.
ISO Tank: ISO Tanks generally come in a standard size of 20 feet and can carry up to 26,000 liters. Because they are standardized, their capacity is fixed across most operations.
Using ISO Tanks provides greater capacity, making them ideal for long-distance or large-volume shipments, particularly when intermodal transport (road, sea, rail) is utilized. In contrast, Lorry Tanks are more suited for local deliveries with smaller volumes or tailored to specific customer requests.
4. Flexibility in Transport
Lorry Tank: Lorry Tanks are transportation systems that operate on roads. They offer flexibility within the constraints of road infrastructure and are particularly efficient for regional and domestic deliveries; however, they are not suitable for sea or rail transport
ISO Tank: ISO Tanks are highly adaptable and can be utilized across various transportation methods sea, road, and rail without the need to transfer the cargo between different modes. This versatility not only shortens handling time but also decreases the chances of spillage or contamination.
Lorry Tanks are suitable for local direct transport; however, for multimodal shipping particularly in international logistics where goods must transition between ships, trucks, and trains ISO Tanks are a better option as they can be easily relocated.
So, which is the better option for your logistics needs, ISO Tank or Lorry Tank?